
7 Wastes of Lean How to Optimize Resources Lean manufacturing, Lean project, Management
7 Wastes Lean will remove or reduce Waste or Non-Value adding steps in our processes. While waste removal should not be the focus of any lean initiative it will certainly be something that you achieve whilst seeking to implement the principles of lean manufacturing.

Los 8 desperdicios en la filosofía Lean Construction Cursos online
Low prices on millions of books. Free UK delivery on eligible orders. Browse new releases, best sellers or classics & find your next favourite book
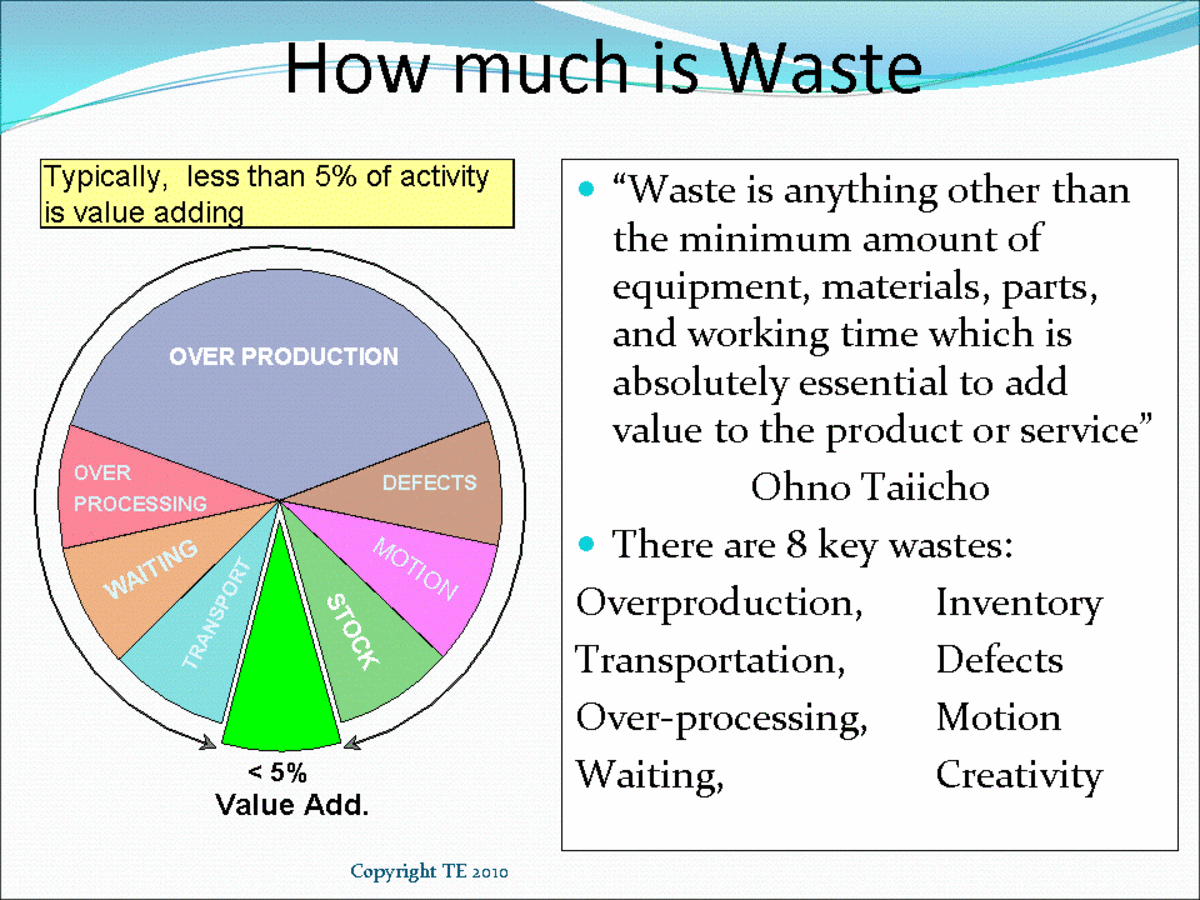
7 Wastes The Seven Muda ToughNickel
Muda, The Seven Wastes Muda is any activity or process that does not add value; a physical waste of your time, resources and ultimately your money. These wastes were categorized by Taiichi Ohno within the Toyota production system, they are; Transport; the movement of product between operations, and locations.
24+ Ide Terkini 7 Mudas Lean Manufacturing
The 7 Wastes of Muda are as follows: Overproduction: Producing more than is needed. Waiting: Waiting for materials, instructions or processes. Transportation: Moving products, materials or people unnecessarily. Over -processing: Using too much processing time or resources. Inventory: Having too much inventory on hand.
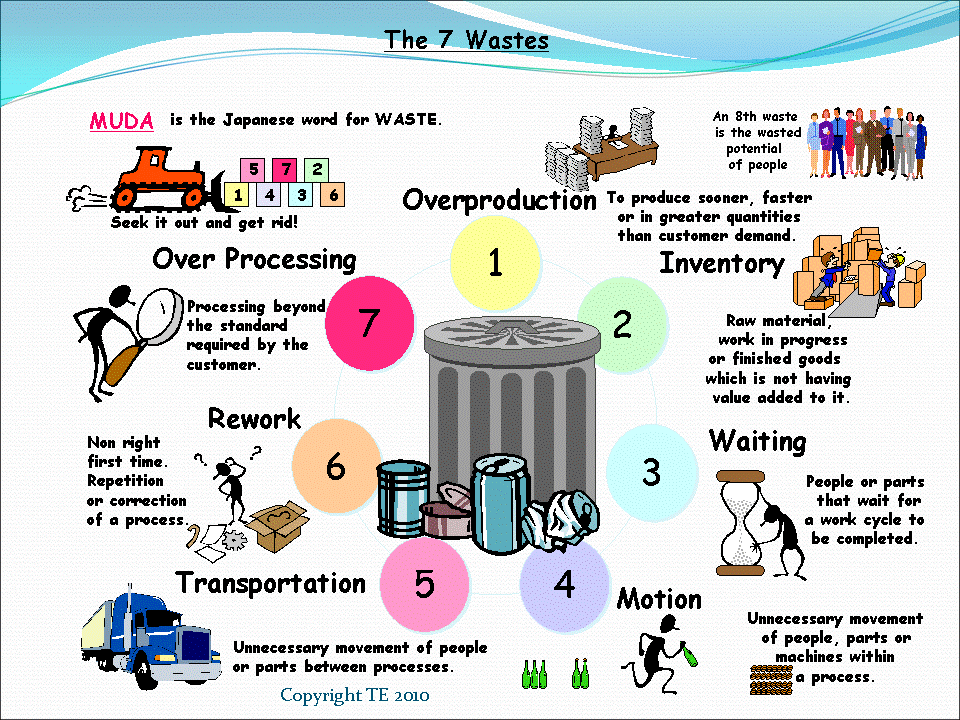
Seven Wastes 7 Mudas of Lean Manufacturing
The seven wastes of Lean Manufacturing are what we are aiming to remove from our processes by removing the causes of Mura and Muri as well as tackling Muda directly. But what exactly are the seven wastes of Lean Manufacturing (or 7 Mudas)? The Seven Wastes of Lean Manufacturing are; Transport Inventory Motion Waiting Over-Processing Overproduction

20+ Konsep Top Les 7 Muda
Global Lean Leader Opex Director. Many people ask me about examples of Mudas (wastes) on 3 main categories, Manufacturing , Office and Supply Chain; for that reason I always share the next table.
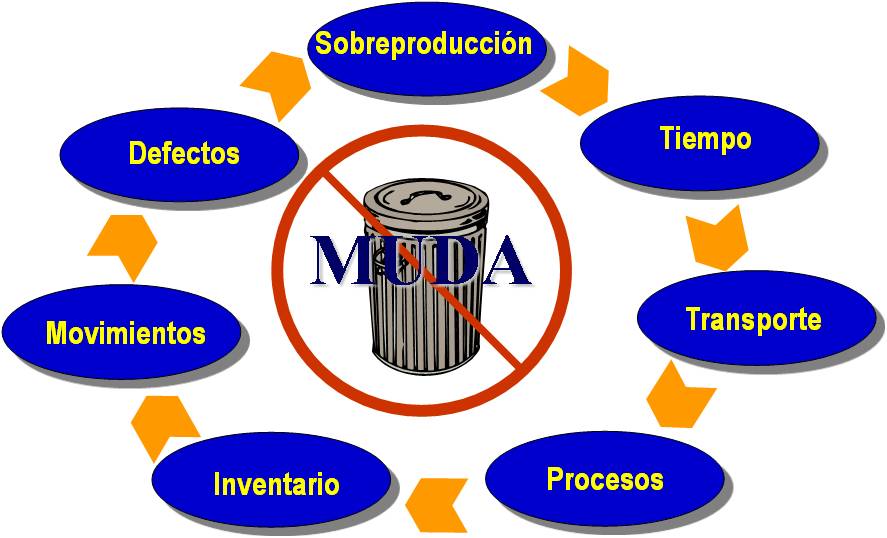
INNOVACIÓN Y PRODUCTIVIDAD Conferencia de Masaaki Imai
Toyota divides Muda into seven resources that are frequently wasted: 1) Transportation — a cost that adds no value to the product but increases the risk of a product being damaged, lost or delayed; 2) Inventory — a capital outlay that if not processed immediately produces no income; 3) Motion — any damage inflicted through the production process.

Kaizen Wheel Kaizen, Classroom organisation, Social science
There are 7 types of muda commonly identified in lean manufacturing: Overproduction Waiting Transportation Overprocessing Movement Inventory Making Defective Parts An eighth type of muda is generally considered in modern lean manufacturing although it was not part of the original Toyota Production System: Unused skills and knowledge 1.

7 Mudas SPC Consulting Group
The Waste of Waiting . Waiting is one of the seven wastes of lean manufacturing (or 7 mudas), it is the act of doing nothing or working slowly whilst waiting for a previous step in the process. How many times have you seen operators stood waiting for a previous operation, a delivery of products to arrive or just slowly working so as not to highlight that they have run out of materials.
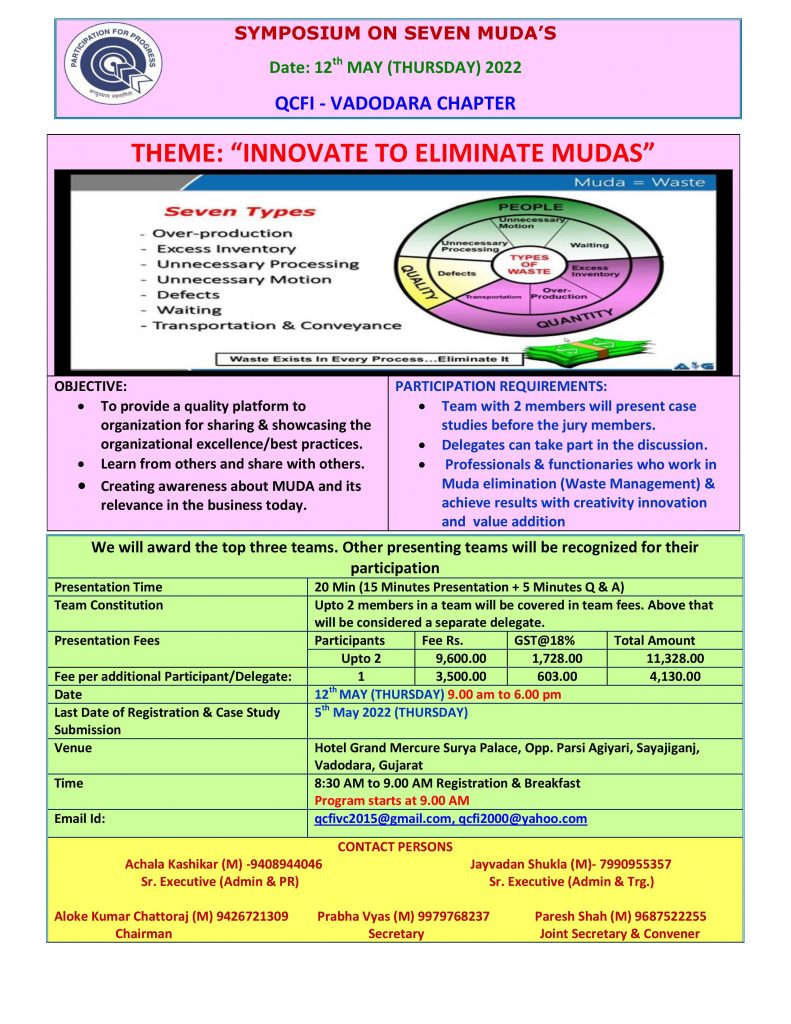
Flyer 7 Mudas QCFI Quality Circle LQC 5S Kaizen Total Quality Management Training
The Toyota Production System, the precursor of Lean Manufacturing and Kanban, identified 7 Mudas or Wastes: Transportation, Inventory, Motion, Waiting, Overproduction, Overprocessing, and Defects. As the system has evolved and been adopted in knowledge work sectors, an 8th Muda has been added to the list: the waste of human potential.
Las 7 Mudas Método Kaizen PDF Economias Procesos de negocio
The 7 forms of muda: Waste of overproduction (largest waste) Waste of time on hand (waiting) Waste of transportation Waste of processing itself Waste of stock at hand Waste of movement Waste of making defective products Muda must be identified in order to be eliminated The two key forms of wastes are obvious wastes and hidden wastes.
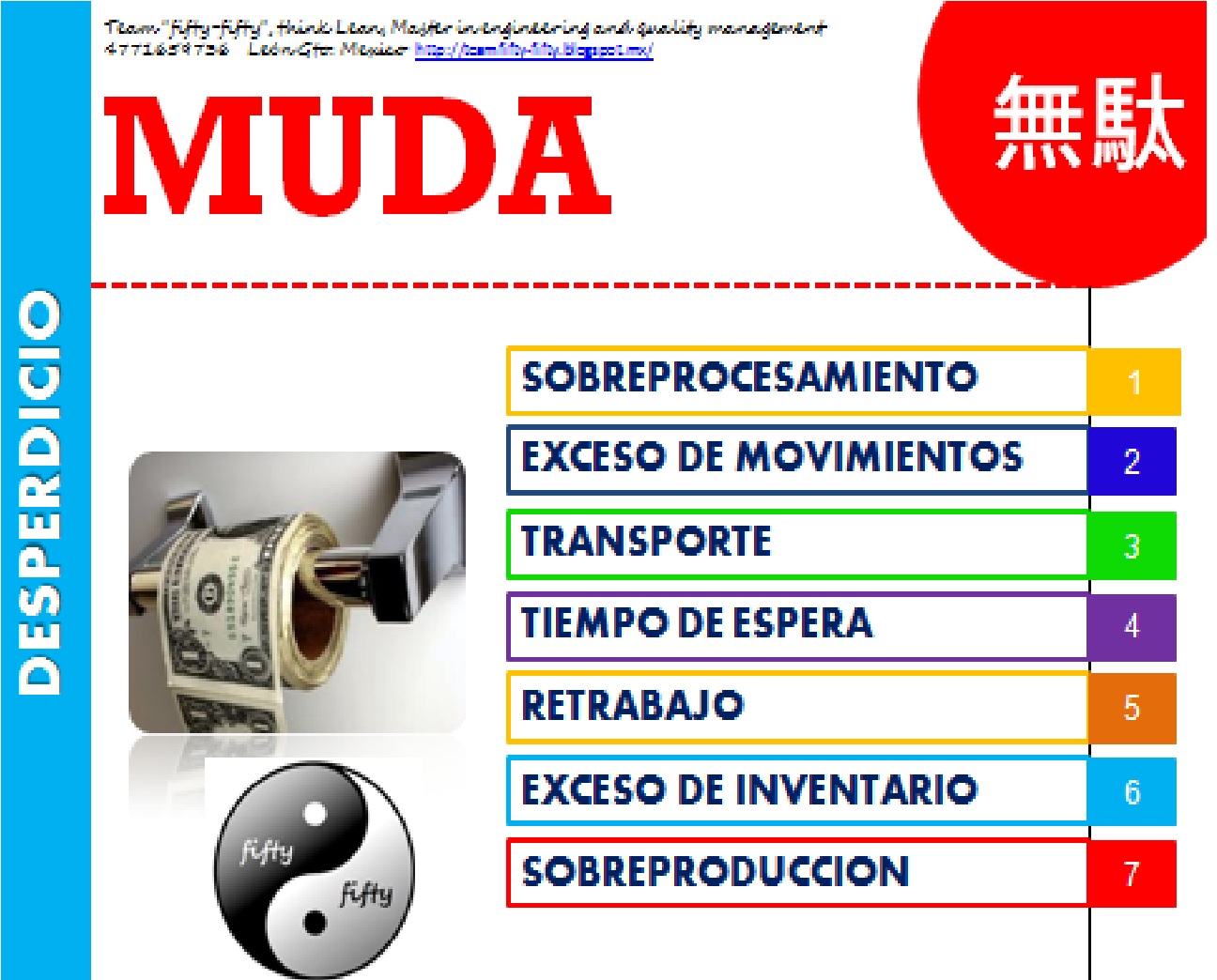
Think Lean, Think in Kaizen 7 MUDAS
The 7 wastes constitute 'muda' and were originally articulated by Toyota's Chief Engineer, Taiichi Ohno. They are a core part of the Toyota Production System, now more widely known as Lean Production, or Lean Manufacturing. We recently looked at another Lean Production tool, Kanban.

7 Waste (Muda) video by Advance Innovation Group YouTube
What are the 7 MUDA (7 WASTES)? by Dante Garcia on June 14, 2019 One Comment Upkaizen School Changing business for the better Recent Cases What they say Laverne Angela Gadiah Thank you for a very clear, easy to follow and concise course. It was informative and definitely on point. Cristyn Narciso
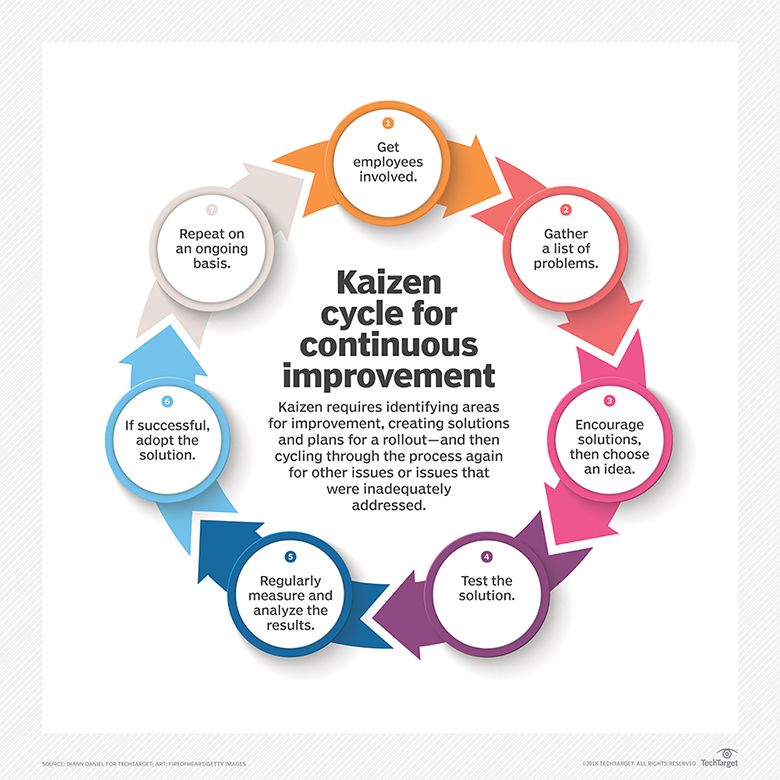
May this be the Kaizen week! King DMC
Based on his observations and deep analysis, he categorized the 7 types of waste (7 Mudas), which later became a popular practice for cost reduction and optimizing resources. What Is Muda (Lean Waste)? Waste in Lean is any activity that consumes resources but brings no value to the end customer.

7 Mudas Kaizen
Lean Management Lean 6 Sigma In order to integrate this into the company culture, Leadership, Daily Management System and Team Performance are crucial for success. Lean Production, the 7 wastes and the KAIZEN meaning Lean Production originates from Toyota.

The Seven Muda (Seven Wastes) Lean Six Sigma Complete Course. YouTube
7 MUDA "Waste!" We Help Operations Managers to Conceive and Actualize Their Industrial Visions Based on the Lean Manufacturing Culture Open menu About Us The 10 good reasons to choose Lean University Our References Lean Trainings Our Training Sessions Lean Trainings calendar Dojo Company Visits Japan Study Tour Custom training Lean Trainings Paths